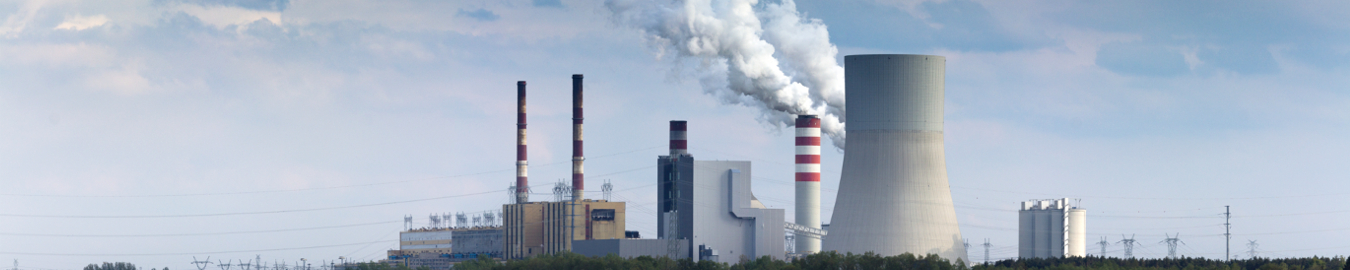
Photovoltaic modules

ENAP offers photovoltaic power plants supplied as components for self-assembly as well as ready-made „turnkey” solutions starting from the project preparation and ending with commissioning and putting into operation. We provide components such as photovoltaic panels, batteries, control systems, inverters and supporting poles.
.
Solar cells are made of pure silicon ore. Plates are made of pure quartz sand which are layered and stapled with electrodes as the basis of a solar cell. These layers generate an electric field whose charges are divided into negative and positive. After separation they accumulate on two opposite poles of the link. Sunlight shining on the cell releases electrons from silicon atoms. A photovoltaic effect is created. Through connected electrodes creates an electric current. To deepen the absorption of sunlight photovoltaic cells are covered with anti-reflective coating. This technology of cell production makes them tight, waterproof, resistant to high levels of UV radiation, moisture and extreme temperatures. The maintenance of the equipment provided by us consists primarily of checking the condition of photovoltaic panels in terms of their mechanical damage related to weather conditions (hail, storms, etc.). All panels are connected with chain links called “strings”. The second important maintenance is cleaning the surface of the panels from dirt associated with atmospheric dust. This should be done at least once a month.
.
SEARCH
NAVIGATION
MARKET
OUR ACTIVITIES INCLUDE
..
..
..
» Industry
» Paper
» Power engineering
» Chemical
» Preparation of project documentation
» Gathering of required equipment
» Producing of prefabricates
» Delivery of materials and installation
» Programming of control drivers
» Conducting of adjustment
» Mechanical and technological start-up
» Preparation of project documentation
.
.
Firma ENAP S.A. uzyskała dofinansowanie z Unii Europejskiej ze środków Europejskiego Funduszu Rozwoju Regionalnego oraz z budżetu państwa na realizację projektu w ramach działania 1.5 RPO WM 2007-2013, pt: „Budowa oraz unowocześnienie zaplecza produkcyjno-usługowego na potrzeby uruchomienia produkcji urządzeń elektroenergetycznych wykorzystujących odnawialne źródła energii oraz usług w zakresie badań certyfikacyjnych”. Informacje źródłowe na temat Regionalnego Programu Operacyjnego Województwa Mazowieckiego 2007-2013 znajdują się na stronie: www.mazowia.eu
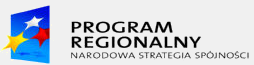

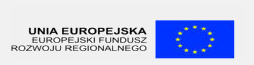